35kV 46kV Power Transformer
- Primary Voltage Ratings 35kV, 34.5kV, 33kV, 46kV or others
- Secondary Voltage Ratings 13.8kV 6kV 10kV or others
- H.V. Tap Range ±8×1.25% or others
- Type Oil-immersed power transformer
- BIL 200kV
- Standards IEEE, ANSI, IEC
- Application Access to urban power grids, industrial and mining enterprises, wind power and photovoltaic power etc
- Power Rating 5000-400000kVA
- Certificate UL ,ISO,KEMA,CESI
- Cooling Method ONAN/ ONAF
- Opeartion Step Down & Step Up
Technical Specifications
Rated Power | 5000-400000kVA |
Rating Primary Voltage | 35kV, 34.5kV, 33kV, 46kV |
Secondary Voltage |
6.6kV 10kV 13.8kV Customized |
Frequency | 50/60Hz |
Vector Group | Dyn11, YD11, YNd11 |
Winding Material | Aluminum/Copper |
Efficiency | As IEEE, CAS Std or Customized |
Impedance Voltage | As IEC |
Altitude | ≤1,000m or Customized |
Enclosure material | Mid Steel |
HV Bushing |
LV Bushing |
OLTC/NLTC |
Lifting hook for complete transformer |
Name plate |
Oil temperature |
Winding temperature |
Radiators |
Oil level |
Pressure relief valve |
CT |
Customization Optional
Packing and Shipping
First, the transformer will be reinforced with high-strength wood and steel materials to ensure its safety during transportation. When packaging, each component will be strictly shock-proofed to prevent any damage during long-distance transportation. The outside of the transformer will also be covered with waterproof materials to resist the influence of wet weather.
To ensure safety during transportation, appropriate insurance will be purchased to cover accidental losses that may occur during transportation. The insurance cost will be calculated based on the value of the transformer and the risk level of the transportation route. We choose to transport through an internationally renowned logistics company to ensure that the entire process is traceable and that any problems that may occur are handled in a timely manner.
During transportation, all equipment and components will be clearly marked for inspection and receipt by the staff at the destination. In order to avoid errors during transportation, detailed transportation documents will be provided to ensure that each link is properly recorded and tracked. The transportation time of the transformer is expected to be 10 to 15 working days, and the specific time will be adjusted according to actual conditions. Upon arrival at the destination, the transformer will be unloaded and inspected by professionals to ensure that there is no damage.
The entire transportation process will be carried out in strict accordance with international standards to ensure that the transformer can reach the customer safely and on time. We believe that through this series of packaging and transportation measures, customers can receive intact transformers to meet their usage needs.
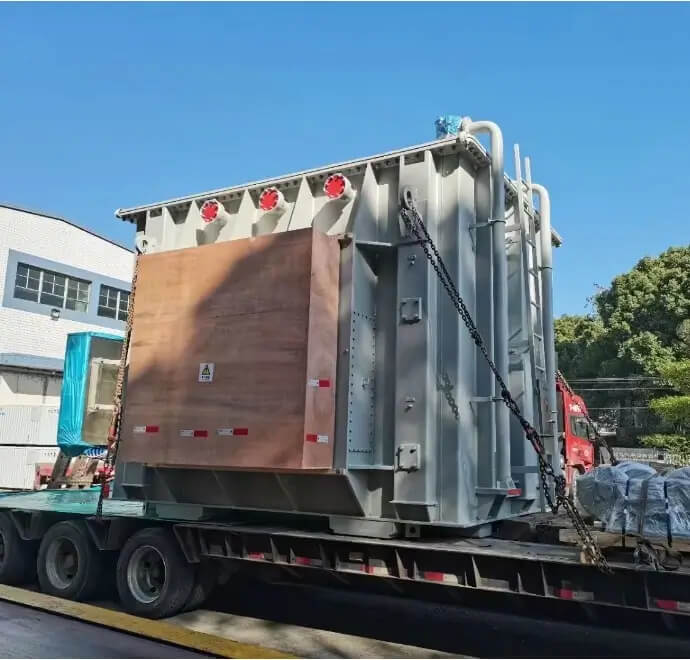
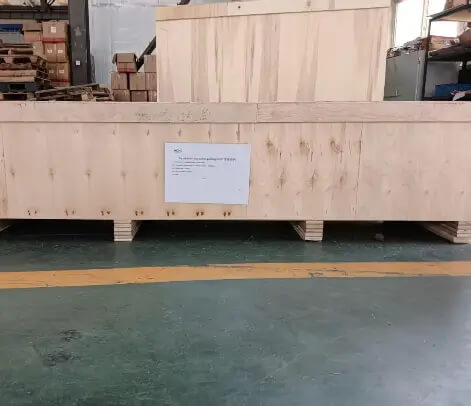
Manufacturer Test
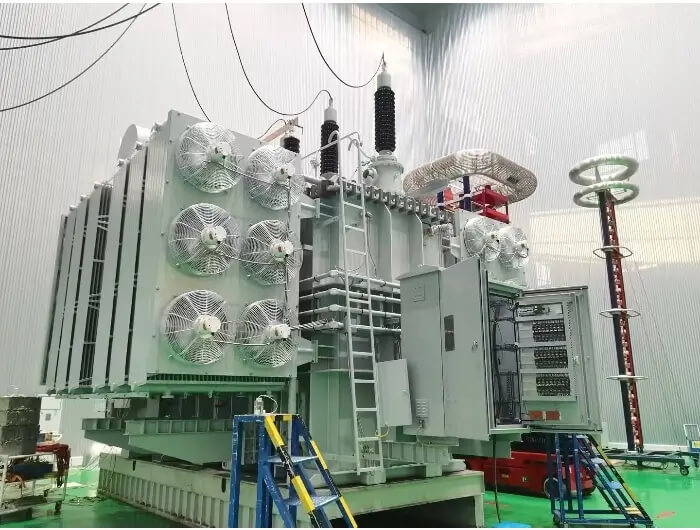
Progress test
The manufacturer's progress test of the NPC ELECTRIC 35kV, 46kV power transformer includes a number of key test procedures to ensure the performance, stability and safety of the equipment. First, the manufacturer will conduct a comprehensive inspection of the mechanical structure of the transformer to ensure that it meets the design requirements. Next, a high-voltage test is carried out to verify the insulation performance of the transformer at rated voltage. Subsequently, a load test is carried out to simulate the operation of the transformer under different loads to ensure that it can work stably in actual applications. Then, a temperature rise test is carried out to confirm that the temperature of the transformer is controlled within a safe range during operation. Finally, a full system trial run is carried out to verify whether various functions and parameters meet technical standards to ensure that the transformer can be put into use smoothly.
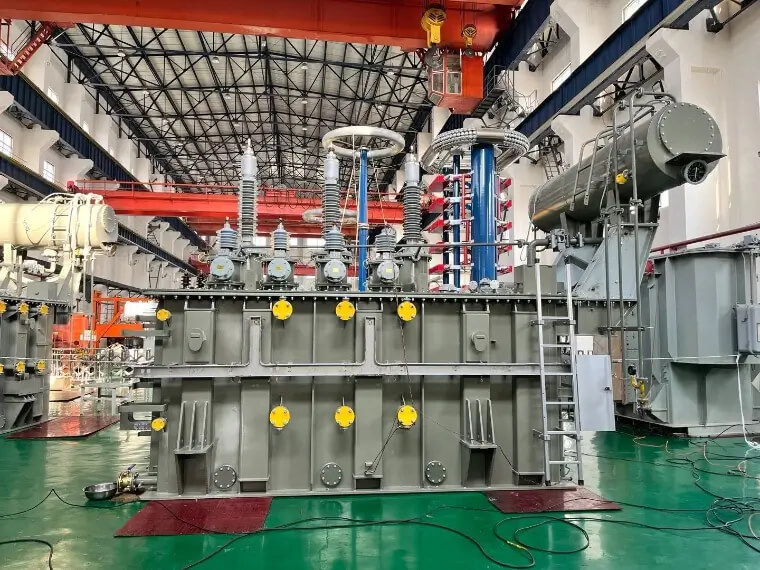
Design Tests
All transformers will be tested after finishing the production test items as below:
♦ Leak testing with pressure for liquid-immersed transformers
♦ Test of transformer oil
♦ Measurement of voltage ratio and check of phase displacement
♦ Measurement of winding DC resistance
♦ Measurement of d. c. Insulation resistance between each winding to earth, and check of the core and frame insulation
♦ Capacitive bushing test
♦ Measurement of dissipation factor (tan δ) of the insulation system capacitances, and determination of capacitances windings-to-earth
♦ Measurement of no-load loss and current at 90%,100%,110% of rated voltage
♦ Operation test on on-load tap-changer
♦ Measurement of short-circuit impedance and load loss
♦ Lightning impulse test
♦ Induced-voltage test with partial discharge measurement
♦ Auxiliary wiring check
♦ Current transformer test
♦ Frequency response analysis test
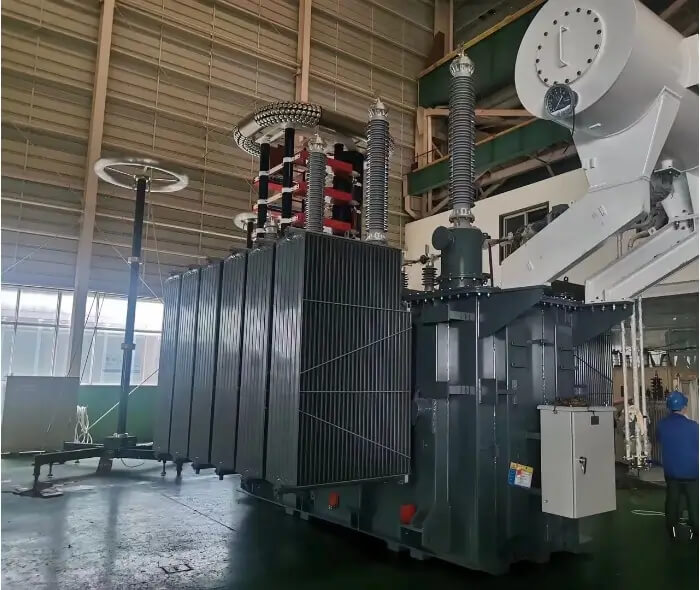
Transformer Factory Acceptance Test
NPC Electric conducts rigorous quality control testing on every transformer or representative samples, as well as on specific components and materials, to ensure compliance with design specifications throughout the production process.
The Factory Acceptance Test (FAT) for a power transformer is a critical step performed before shipment to verify that the unit meets all applicable standards and delivers optimal performance. The FAT includes the following key procedures:
Visual Inspection: Evaluates the transformer’s physical condition, including the enclosure, terminals, and labeling, to ensure conformance with design and safety requirements.
Electrical Testing: Involves measuring winding resistance, insulation resistance, and performing turns ratio tests to validate electrical integrity and functionality.
Dielectric Strength Test: Applies high voltage across the insulation system to ensure it can endure both normal and transient operating voltages without failure.
Load Testing: Simulates real-world operating conditions to assess the transformer’s voltage regulation, temperature rise, and overall efficiency under load.
Protection Device Testing: Verifies the proper operation of integrated protective components such as thermal sensors, temperature relays, and tap changers (if applicable).
Routine Test - Leak Testing With Pressure For Power Transformers
Nitrogen or air source (inert gas)
Pressure relief valve
Vacuum pump (if needed)
Soap solution (for identifying leaks)
Test plugs or sealing components (for test points)
Appropriate safety equipment (gloves, goggles, etc.)
Inspect the transformer’s external components such as bushings, tap changer, and radiator fins to ensure there are no visible external leaks.
Verify that the transformer is at room temperature and that it has been adequately ventilated.
The transformer is de-energized, and all external components such as bushings and tap changers are inspected. All access points, including vent valves and pressure relief valves, are sealed to prevent air or oil leakage during the test.
Applying Pressure:
An inert gas (typically nitrogen) is introduced into the transformer tank, and the pressure is gradually increased to the specified test pressure, typically 1.5 to 2 times the normal operating pressure.
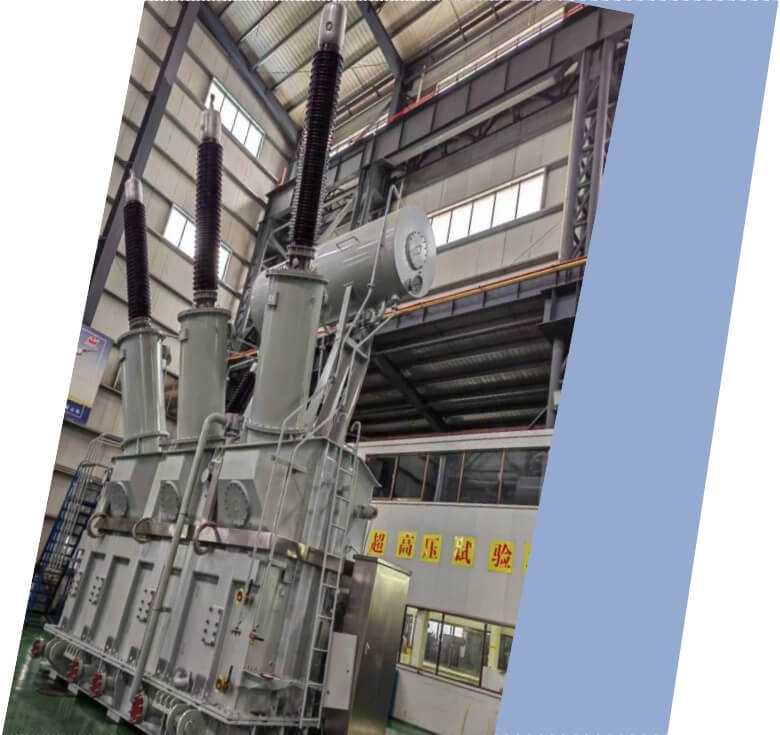
Application
Technical Advantages
Product Packaging
Related Products
FAQ From Customers
-
What is a Transformer?A transformer is an electrical device used to change the voltage of alternating current (AC). It works on the principle of electromagnetic induction, converting high-voltage current into low-voltage current or low-voltage current into high-voltage current. Transformers are widely used in power transmission, distribution systems, and various electronic devices.
-
What are the main uses of a transformer?The main use of a transformer is voltage conversion. Transformers are used in power transmission systems to help transfer electricity from power plants to consumers. In addition, transformers are also used in electronic devices such as chargers, televisions, power adapters, etc., to adjust the voltage to meet the requirements of different devices.
-
Do you have UL listed?Yes, our transformer has UL listed. We have exported to America many pad mounted transformer,substation transformer and HV.